This website uses cookies so that we can provide you with the best user experience possible. Cookie information is stored in your browser and performs functions such as recognising you when you return to our website and helping our team to understand which sections of the website you find most interesting and useful.
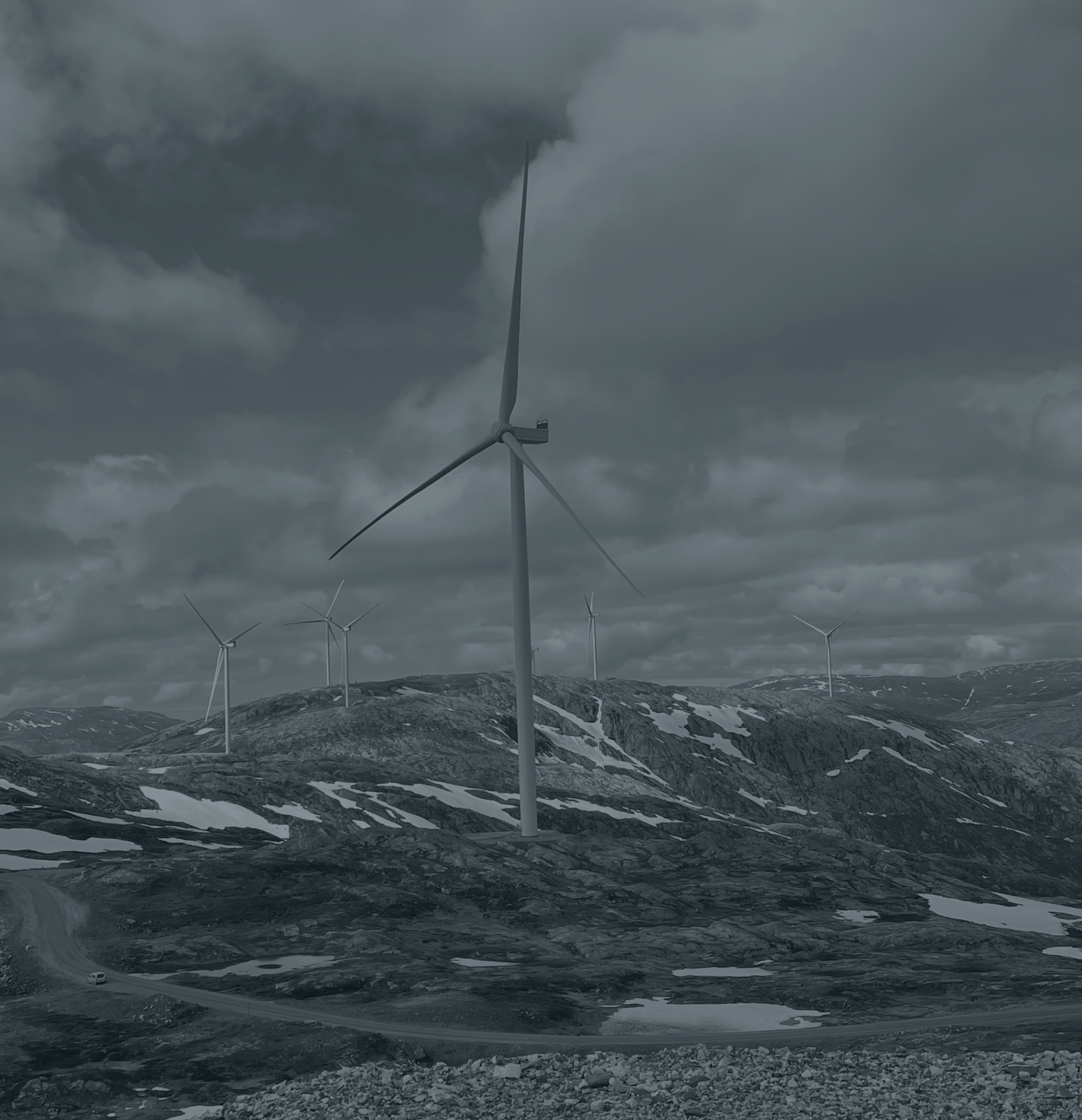
Case study
Transferring Knowledge for the Energy Transition – Windmill Maintenance
Transferring Knowledge for the Energy Transition – Windmill Maintenance
The project comprised inspecting and controlling the active force in rock anchoring bolts, many of which were up to 15 metres long.
“The most beautiful place we have ever worked!”
OVERVIEW
The procedure known as ‘First Maintenance’ of windmill anchoring bolts must take place between 6 – 12 months from the date of installation. With the 12-month deadline on the horizon, our scope was to inspect the windmill foundations and confirm the tension in the windmill rock anchors via bolt testing.
WHAT WE DID
The bolts were tested over two separate two-week periods for damage and corrosion, checking the load in the bold via active force control.
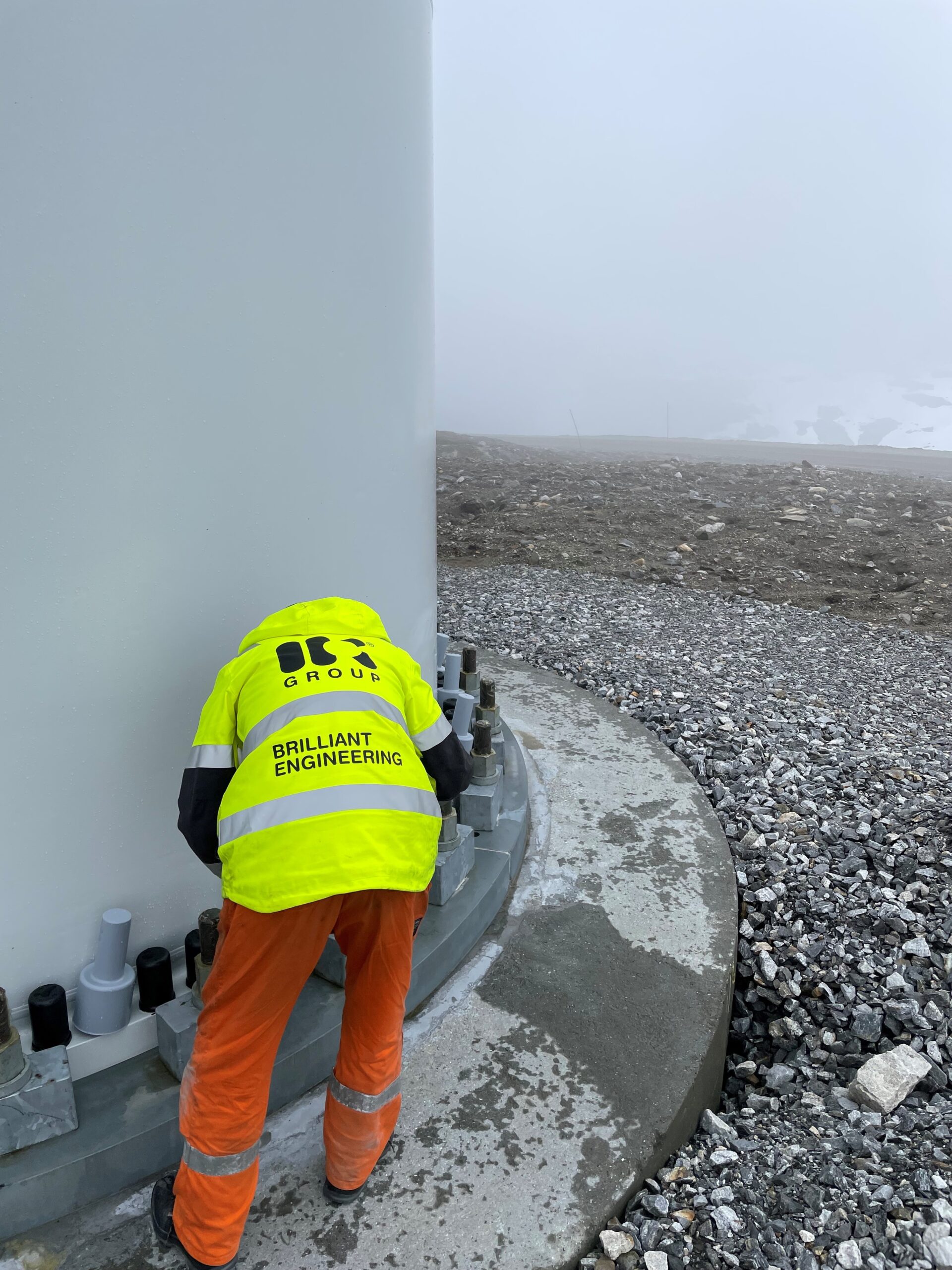
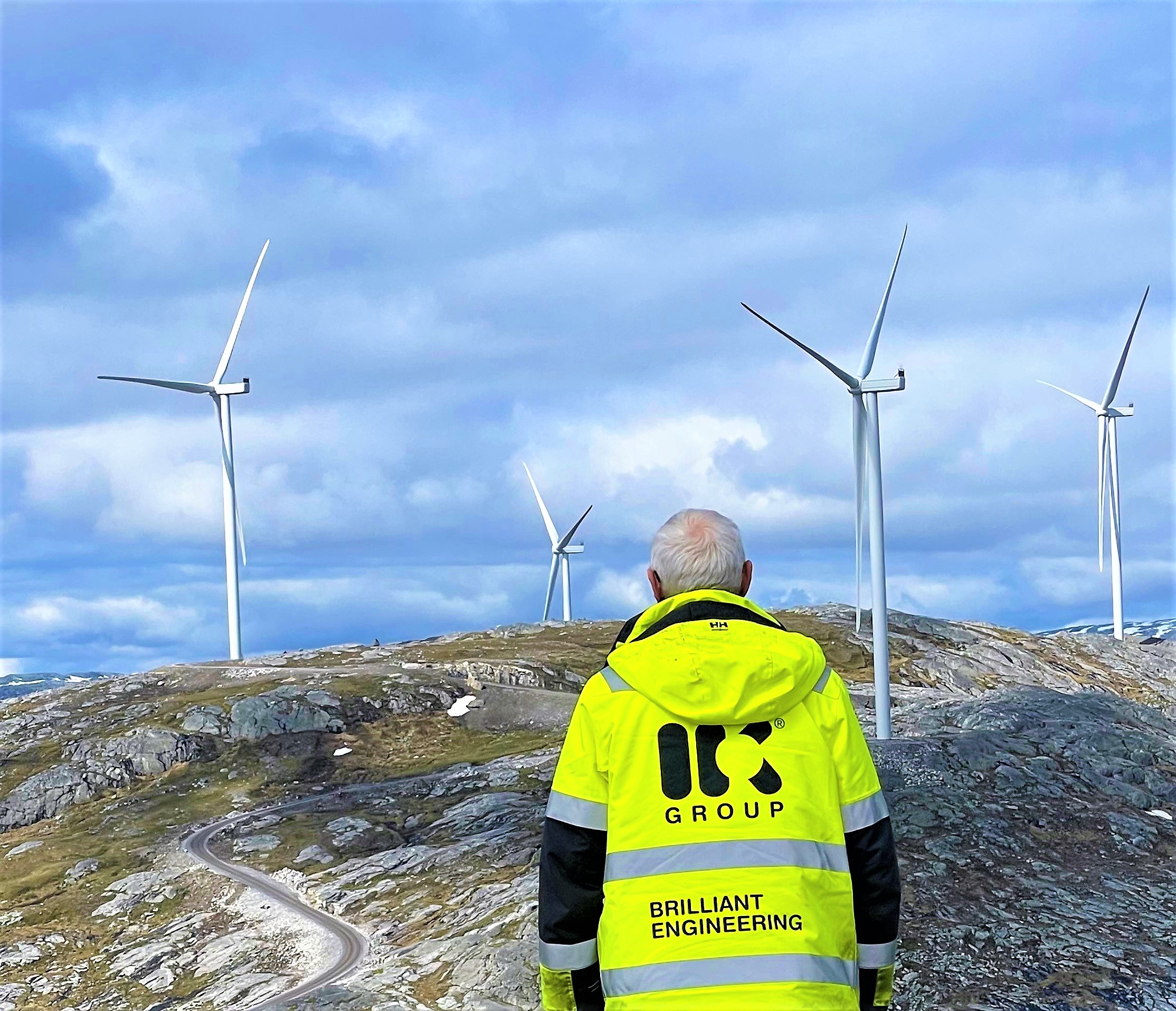
Technical Expertise
With decades of experience in bolt tensioning and torquing on pipeline flanges, our IK TOPSIDE team expertly utilised a rock foundation tensioner, completing the testing of approximately three foundations per day.
Good Project Management Crosses Sectors
IK TOPSIDE is renowned for solving some of the energy industry’s most challenging problems. That’s partly due to our pragmatic, innovative product design, manufacture and deployment – but our project management skills also set us apart. With decades of experience in some of the world’s most dangerous and unpredictable environments, we have developed detailed project planning. This results in steady operations with no downtime and establishes a cast-iron process for dealing with any deviations.
We transfer those project management skills from offshore topsides to renewable energy workscopes. Additionally, we take challenging remote terrain and adverse weather conditions into account, yielding significant results.
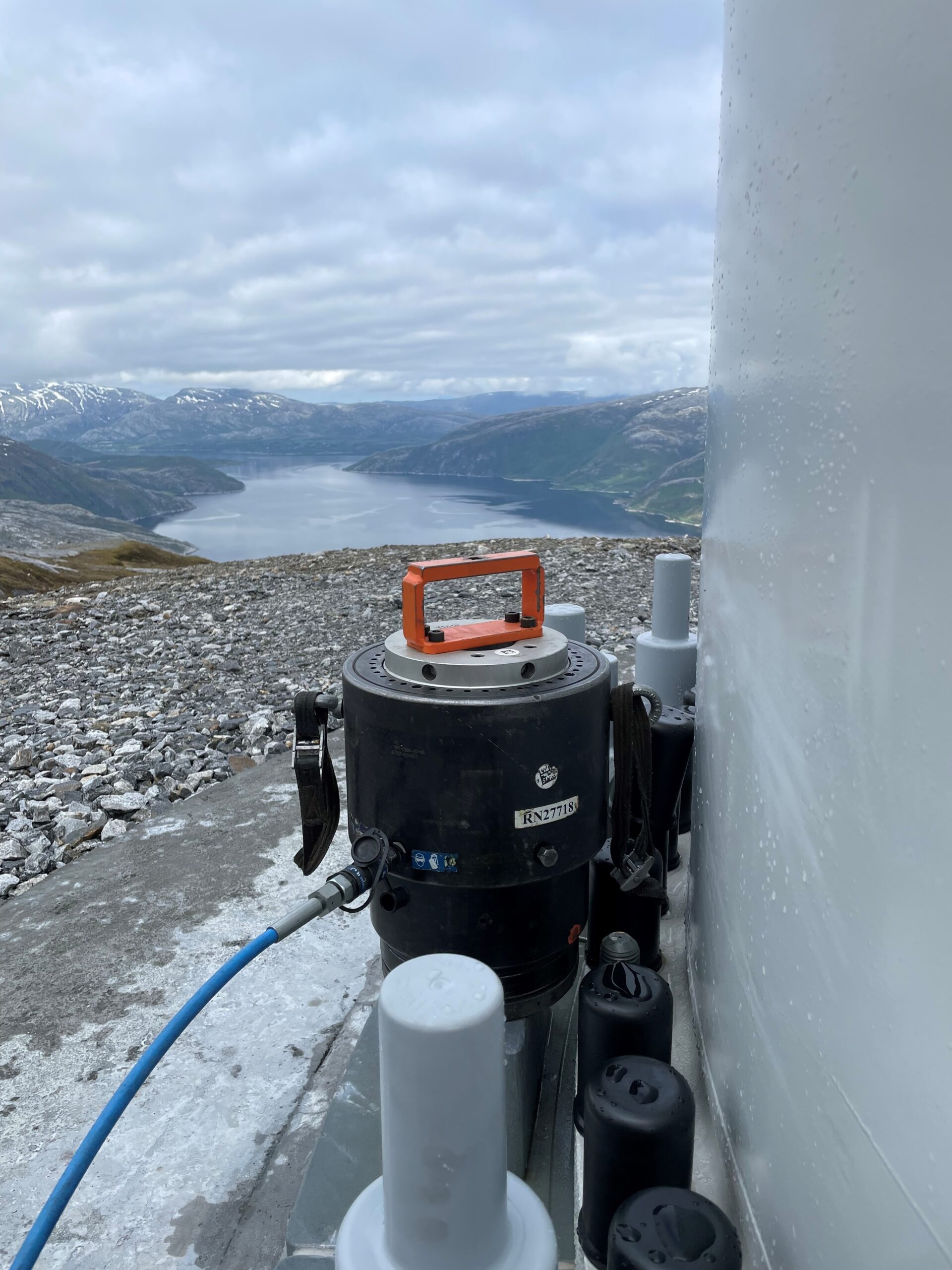
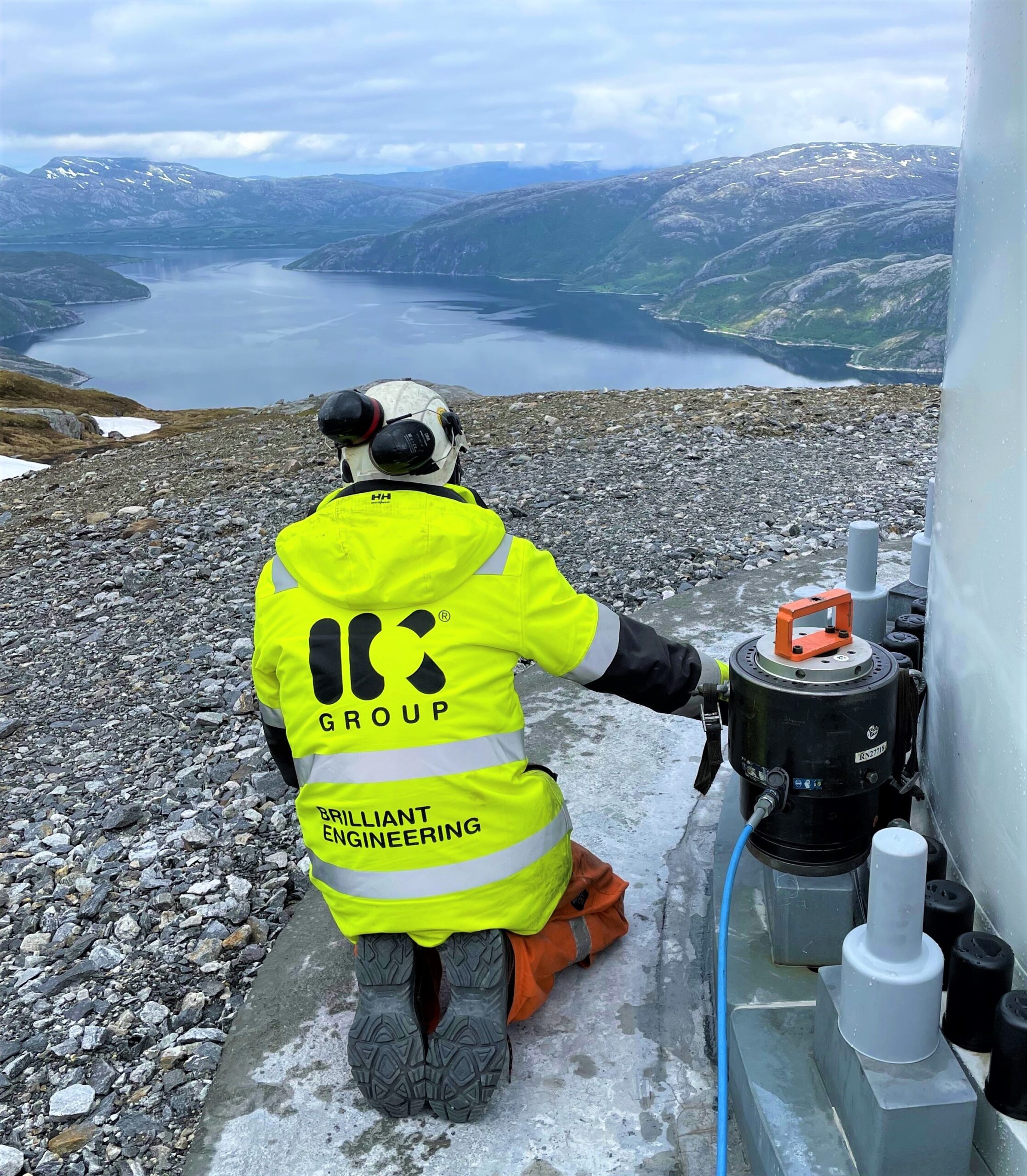
Results
A two-person team worked in close coordination with additional maintenance work onsite, testing a total of 2036 bolts on schedule despite minor deviations due to bad weather and the significant administration required to log the pressure used and the results of testing of each bolt.