This website uses cookies so that we can provide you with the best user experience possible. Cookie information is stored in your browser and performs functions such as recognising you when you return to our website and helping our team to understand which sections of the website you find most interesting and useful.
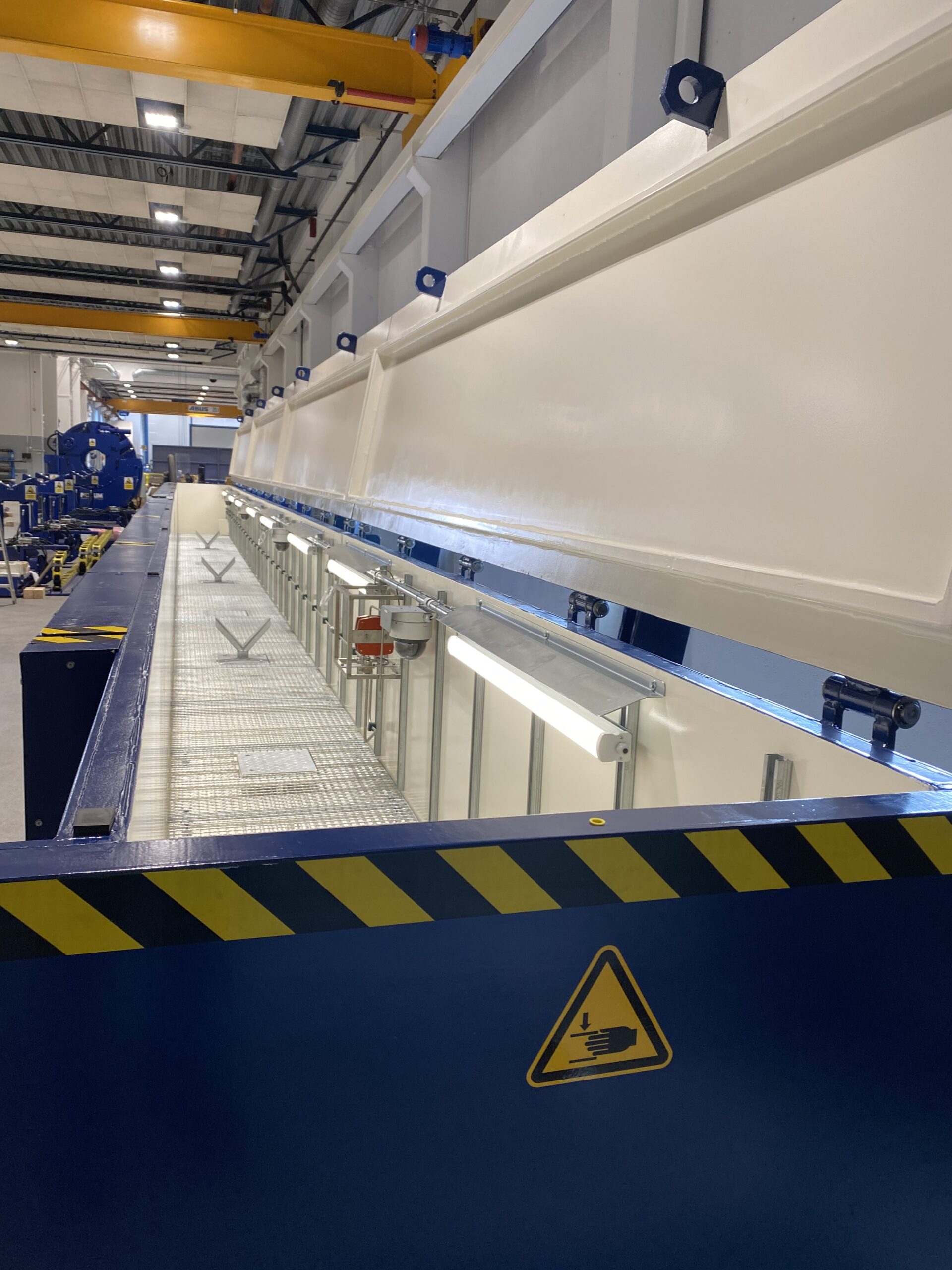
Case study
Effective Partnership and Product Experience – installation of HPU Testbox
Effective Partnership and Product Experience – installation of HPU Testbox
Our client wanted to consolidate its operating locations in one region, and having found a central location suitable for its completion activity, IK TOPSIDE was approached to supply a flexible, self-contained system to the client’s specifications.
We proposed the Test box system – an efficient and cost-effective means of performing safe HPU testing in a modular containment that can be transferred to another location. This also removes the cost of permanently integrating test bays into buildings and workshops.
Overview
What we did
We are experts in supplying and installing standard HPUs with our manufacturing partner, Resato. IK TOPSIDE is Norway’s exclusive Resato supplier, providing a holistic pre- and post-manufacturing service, including survey, project management, delivery, installation, parts, servicing and spares.
Our 12+ years of experience gave the client confidence in our ability to deliver an unusually long test bay – 20m – which would also include in-built safety features specific to their own safety guidelines.
IK TOPSIDE commenced the six-month project with a survey of the test area to ensure that the required asset could be safely integrated into the facility, with future relocation an option.
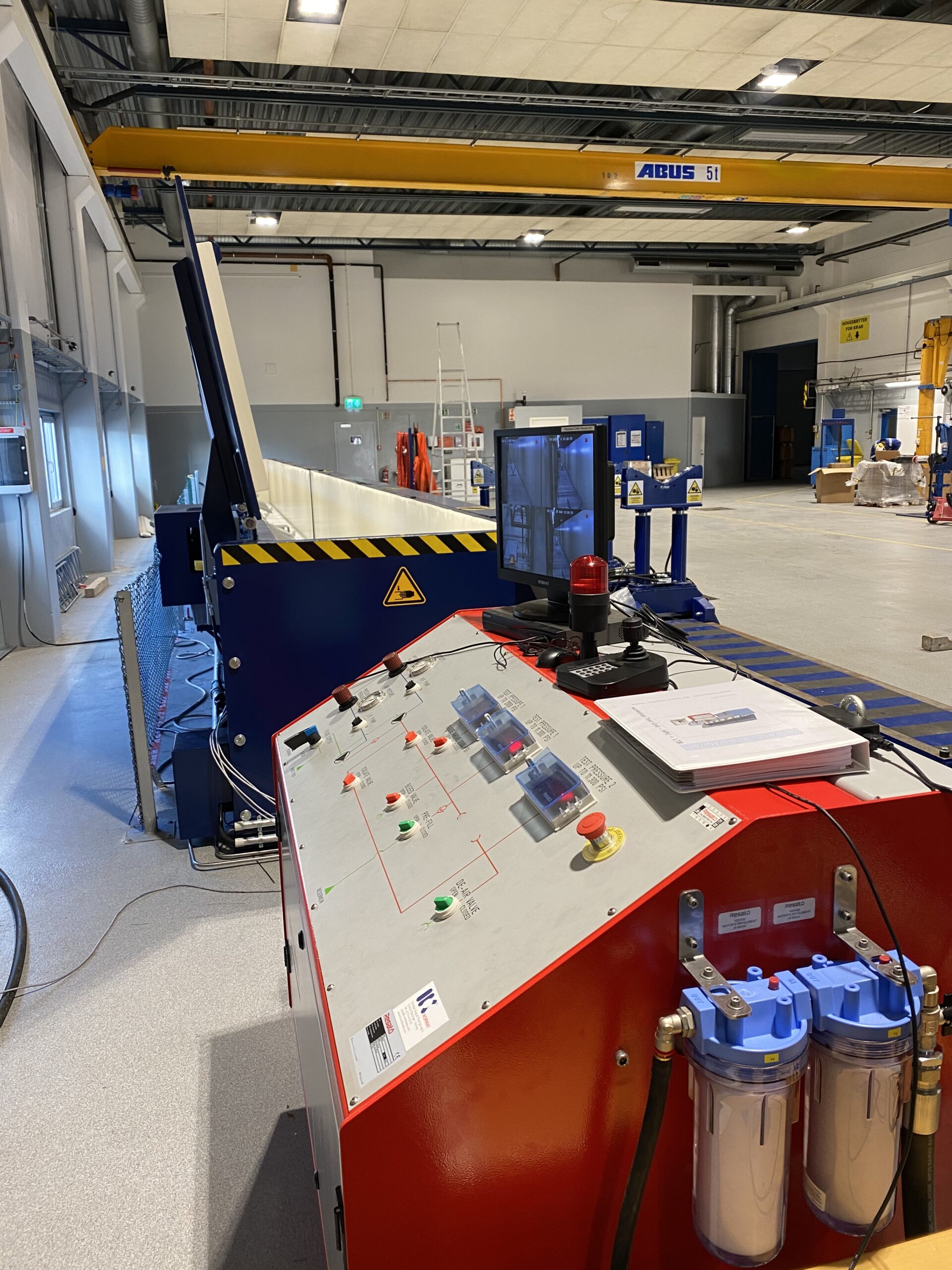
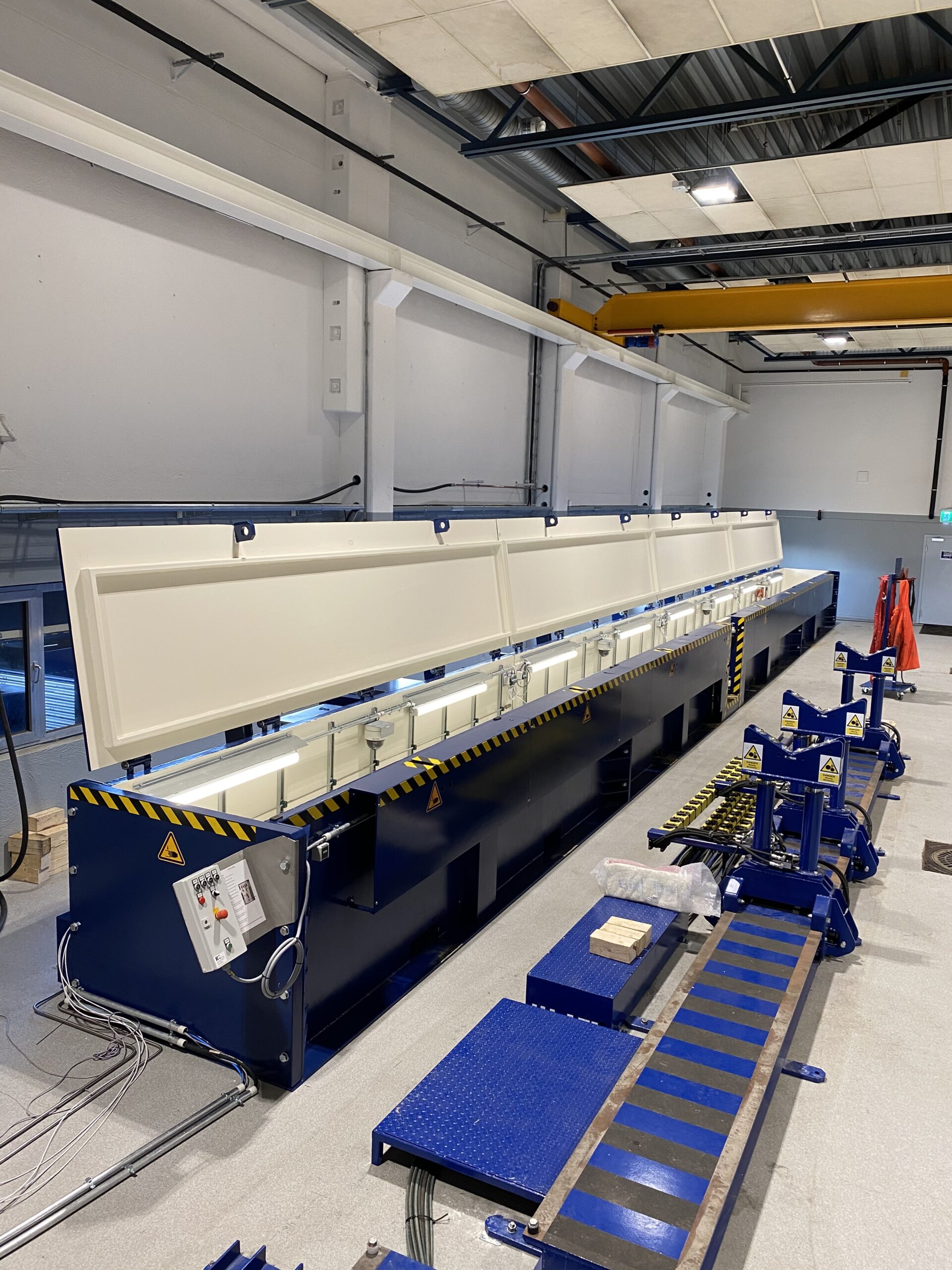
Optimising efficiency and safety
As Resato builds a standard 5m test bay, we commissioned four x 5m test bays to accommodate the required length within the chosen facility, only the second 20m Test box ever to be manufactured and installed.
Self-Contained System
We commissioned a self-contained system with a pre-fill skid and high-pressure (700 bar), low-volume pump system running through the HPU. By creating a closed loop, the system negated the requirement for any drainage of waste liquid, with all content returning to the pre-fill tank.
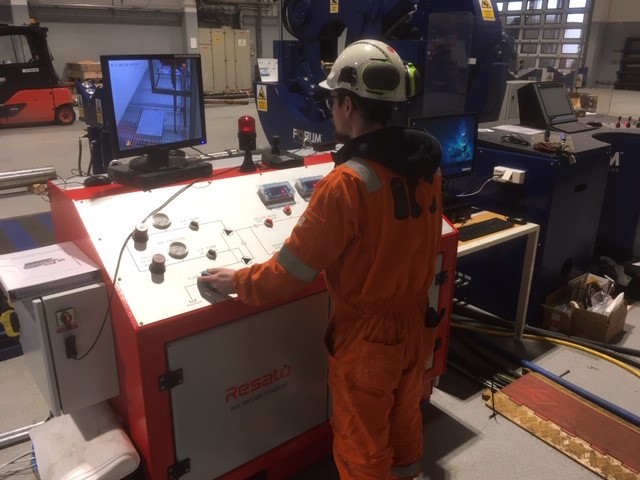
Safety features
During the commission phase, the client’s safety guidelines were reflected in the safety features embedded within the system. IK-TOPSIDE’s experience and understanding of our client’s safety requirements allowed us to adapt the product specification without difficulty to include:
- Lighting
- Locks
- Emergency button
- Cameras
- Pre-fill skids
- Hydraulic drive
- Controlled bleed
- Fast filling time
- Logging system
Project Management
With manufacturing handled by Resato, IK-TOPSIDE’s project management ensured regular communications between all parties to ensure an on-schedule delivery and installation. In addition, IK TOPSIDE:
- Managed and attended FAT with client and Resato
- Delivered and installed the final product, managing all logistics
- Supplied product training to the client
- Produced automated services and calibration reminders, carrying out both activities and providing system verification
- Technical review board
- Design review with relevant personnel
- Regular, frequent communication
- Collaborative spirit with a common objective
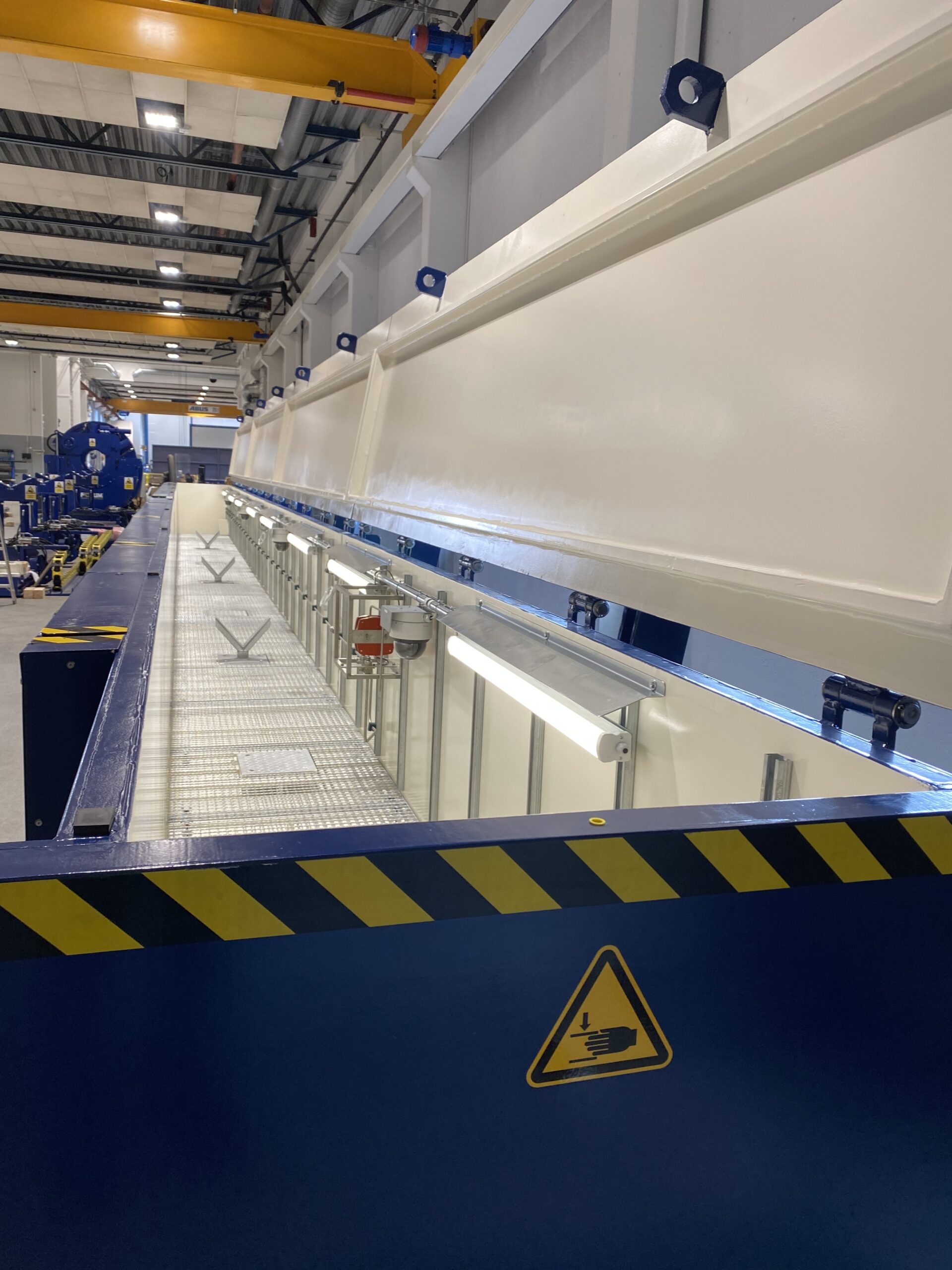
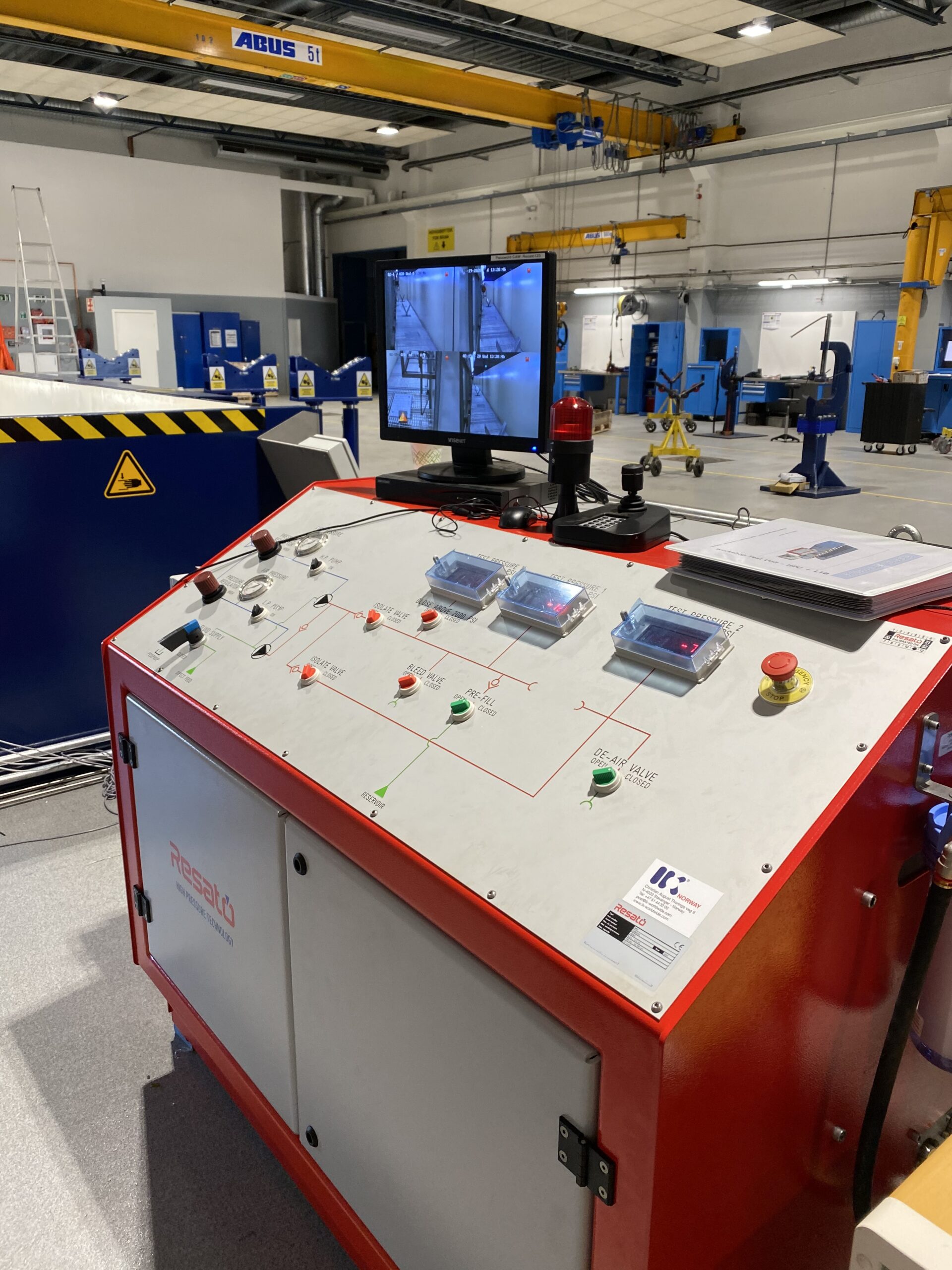
Results
One of just two 20m HPU Test boxes, this project exemplifies our ethos to accept all challenges whilst underlining the strong and trusted working relationship between IK TOPSIDE and Resato.
We aim always to ensure a straightforward experience for our client, with minimal points of contact, creating an efficient and cost-effective process. As a returning customer, our client was confident in our ability to deliver an unusual product with our usual level of service.
The client ordered a second delivery and now operates two similar Testbox systems.