This website uses cookies so that we can provide you with the best user experience possible. Cookie information is stored in your browser and performs functions such as recognising you when you return to our website and helping our team to understand which sections of the website you find most interesting and useful.
Case study
Challenge Accepted! Hot Tapping and Plugging Through Valves
Challenge Accepted! Hot Tapping and Plugging Through Valves
As North Sea assets continue to operate significantly past their original “shelf life”, so maintenance of those assets becomes an increasingly skilled operation. Our client, a late-life asset owner, required expert help to change several outlet valves from an ageing concrete structural support tank with the objective of extending the asset’s productive life.
IK TOPSIDE was identified as the only supplier with the unique combination of expertise and a “can do” attitude to successfully solve this unusual issue.
The situation
A concrete tank, based on an offshore asset, presented a leak. The use of butterfly valves meant that access to the tank was restricted, making it impossible to drain the tank before repair work. Knowing IK- TOPSIDE’s ability to “solve the unsolvable”, we were invited to perform a FEED study, the results of which led to the award of the EPCI offshore contract based on the solutions suggested and our technical know-how.
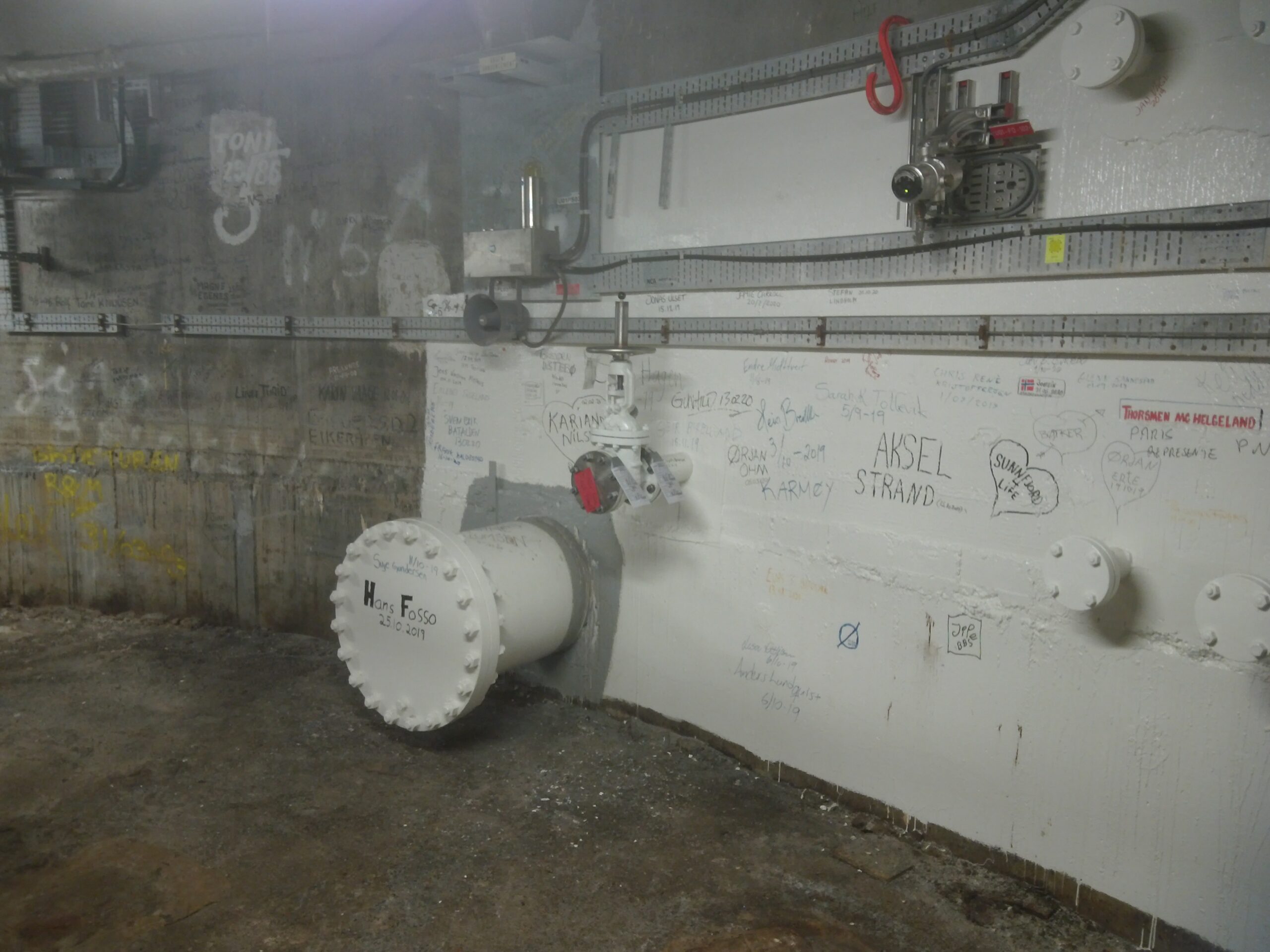
Challenges
This was a unique situation with no precedent to follow. The difficulty came due to a small leak between the butterfly valve – found to be rotten – and its connected flange towards the Triangle cells, making it impossible to empty the tank before tie-in safely.
The presence of hydrogen sulphide (H2S) necessitated the requirement for specialist PPE each time the system was opened.
What we did
Without the possibility of isolating the valve, our unique solution involved hot tapping two 4” butterfly valves, including isolation plugging and valve replacement against the tank.
Hot tapping allowed us to drill out the defective element, remove a previously installed blind flange at the centre of the butterfly valve, and introduce a ball valve and seal adapters against a blind flange to create a safe hot tap barrier, facilitating easy isolation in future.
We installed and activated a double barrier extended hot plug to isolate the tank and replaced the old valve with a new valve while keeping the extended plug activated.
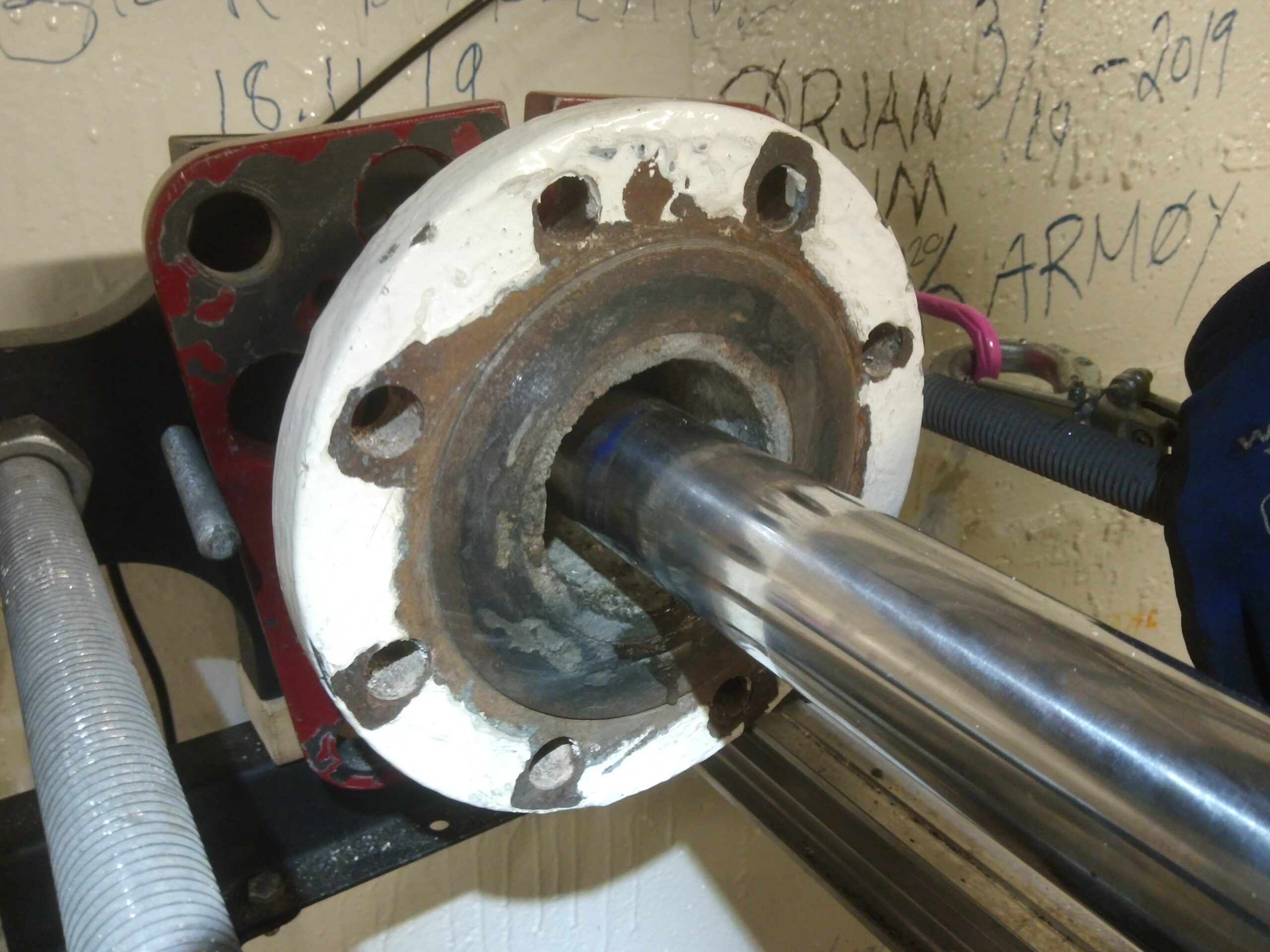
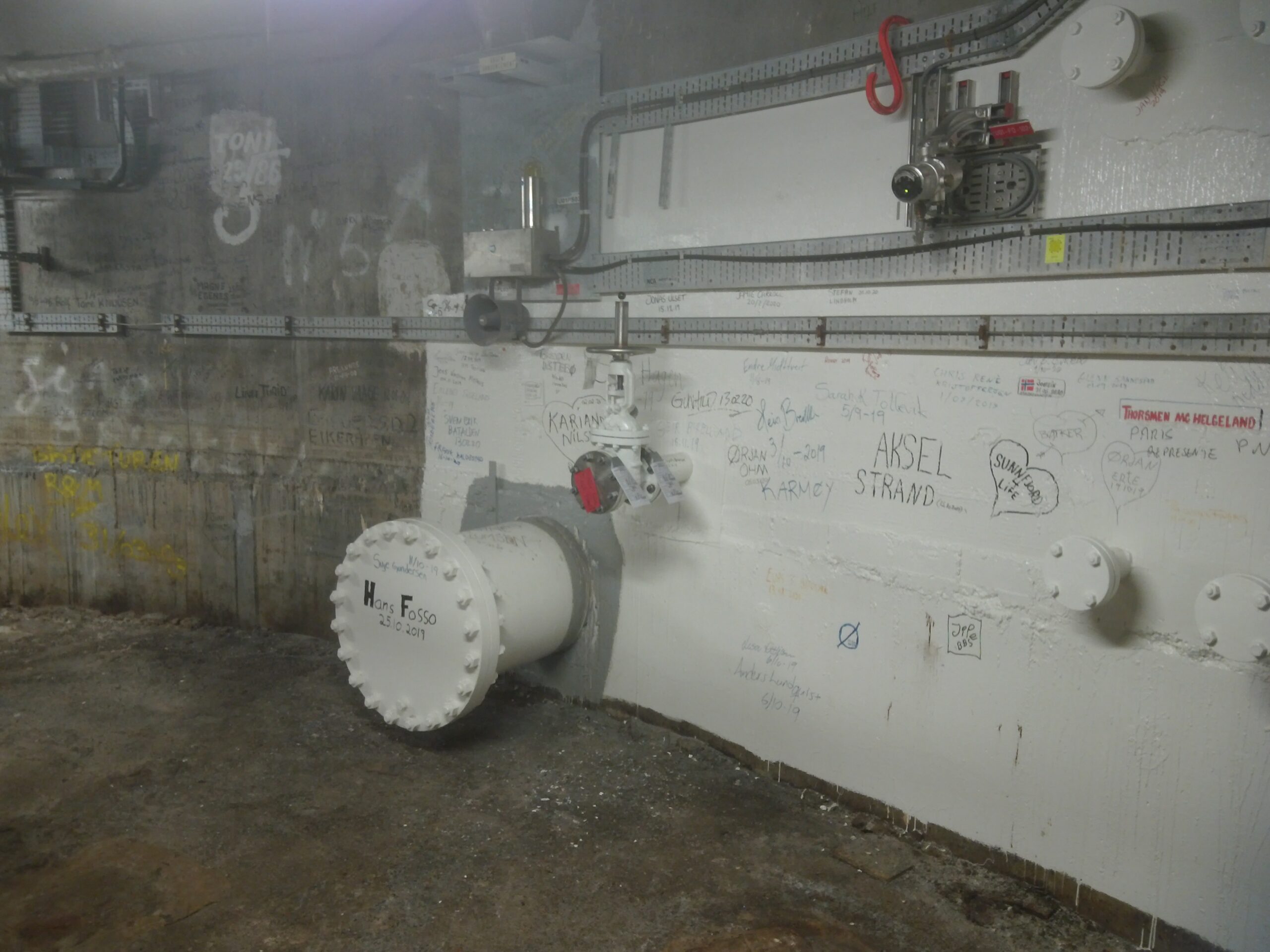
Results
A highly unusual problem, the type we have never encountered previously, this project represents the kind of scenario for which IK TOPSIDE is renowned across the global offshore energy industry.
Drawing upon 30+ years’ experience in solving our client’s most challenging issues, we had the technical expertise and the confidence to deal with the unknown – resulting in the successful resolution of an issue for which there was no known solution.
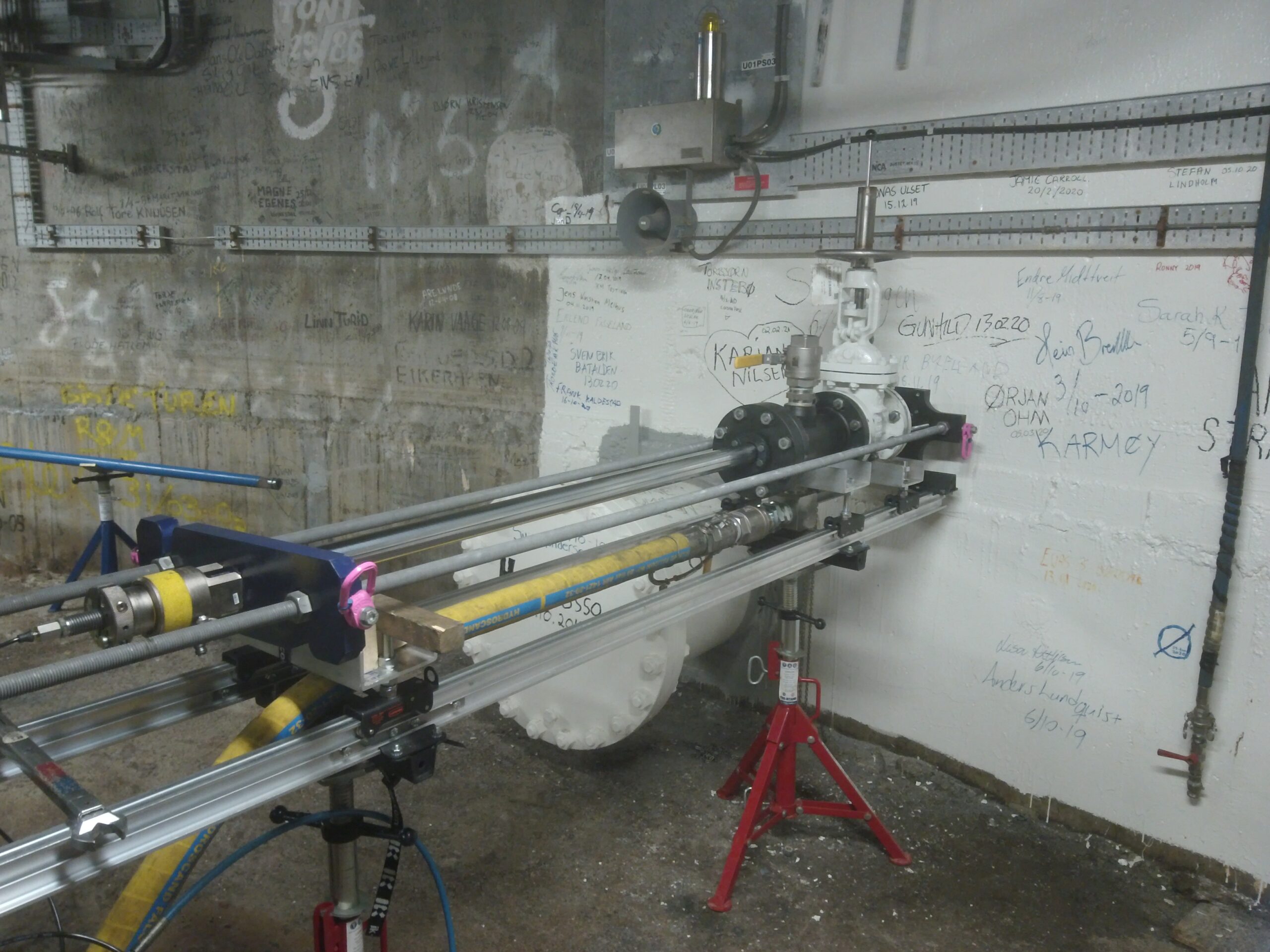