This website uses cookies so that we can provide you with the best user experience possible. Cookie information is stored in your browser and performs functions such as recognising you when you return to our website and helping our team to understand which sections of the website you find most interesting and useful.
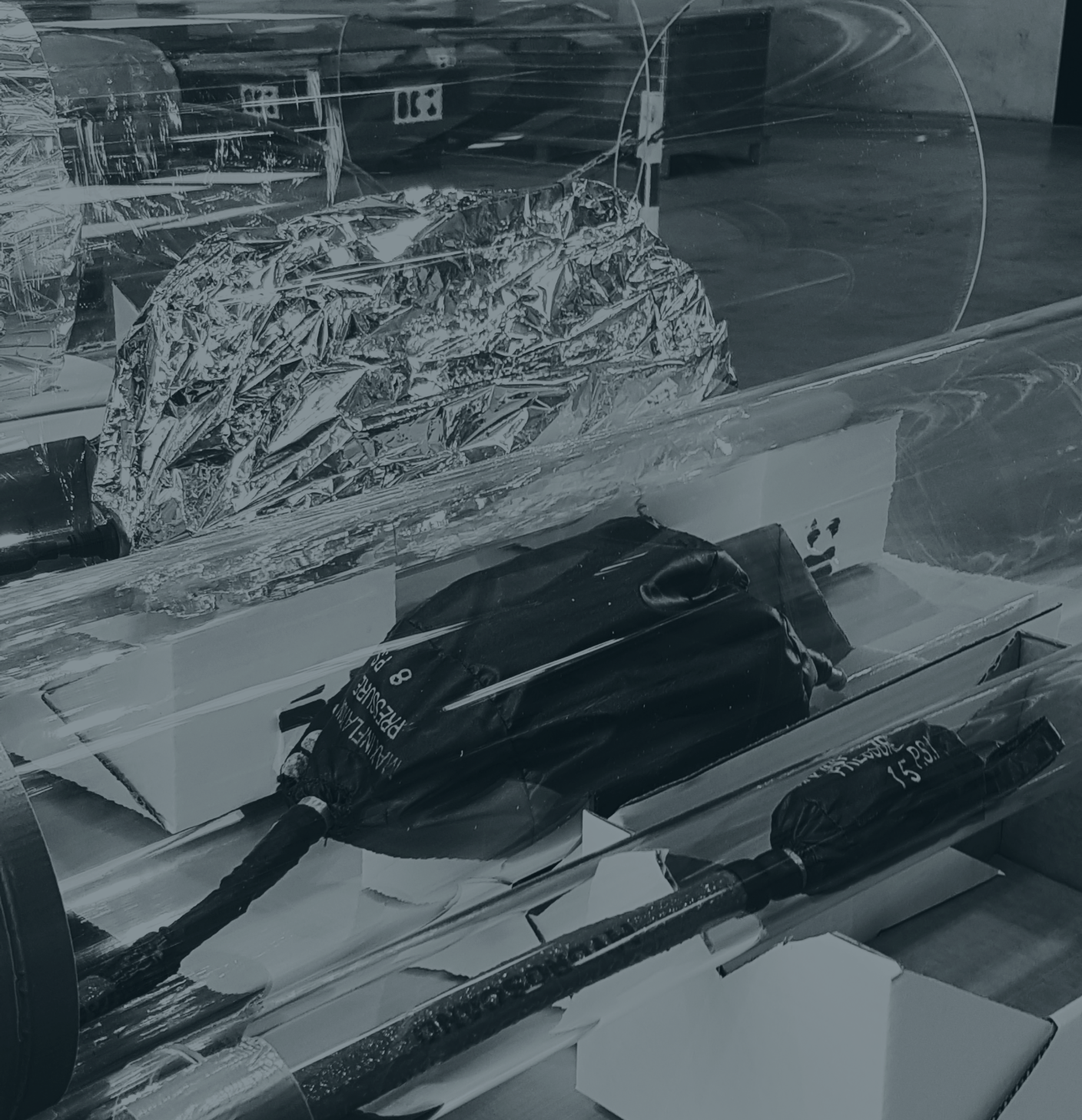
Case study
”An eye-opener for many” – the Valkyrie Back-Gas System Solution
An eye-opener for many” – the Valkyrie Back-Gas System Solution
A tier-one contractor working for one of the North Sea’s largest operators approached IK TOPSIDE, knowing that our specialist knowledge of back-gas possibilities could help solve specific engineering challenges during the hook-up phase of several bridges at the commissioning stage of one of the largest offshore oil & gas installations in Norwegian history. The contractor’s key objective was to avoid the delays and costs associated with redesigning drawings and with flushing and pressure testing of multiple gas pipelines.
Within two months, IK TOPSIDE designed, tested and manufactured three unique back-gas solutions, which mitigated the requirement for flushing and kept the commissioning schedule on track.
Overview
With designed engineering undertaken by several sub-contractors, our client was aware that a lack of communication between all parties had resulted in numerous challenges when it came to the back-gas purging stage and the hook-up of five installations to four pipe-filled bridges.
Due to the installation of long, flangeless lengths of piping with multiple bends, traditional back-gas equipment would be proven impossible to remove after welding via the 1” Threadolet available without flushing the pipelines.
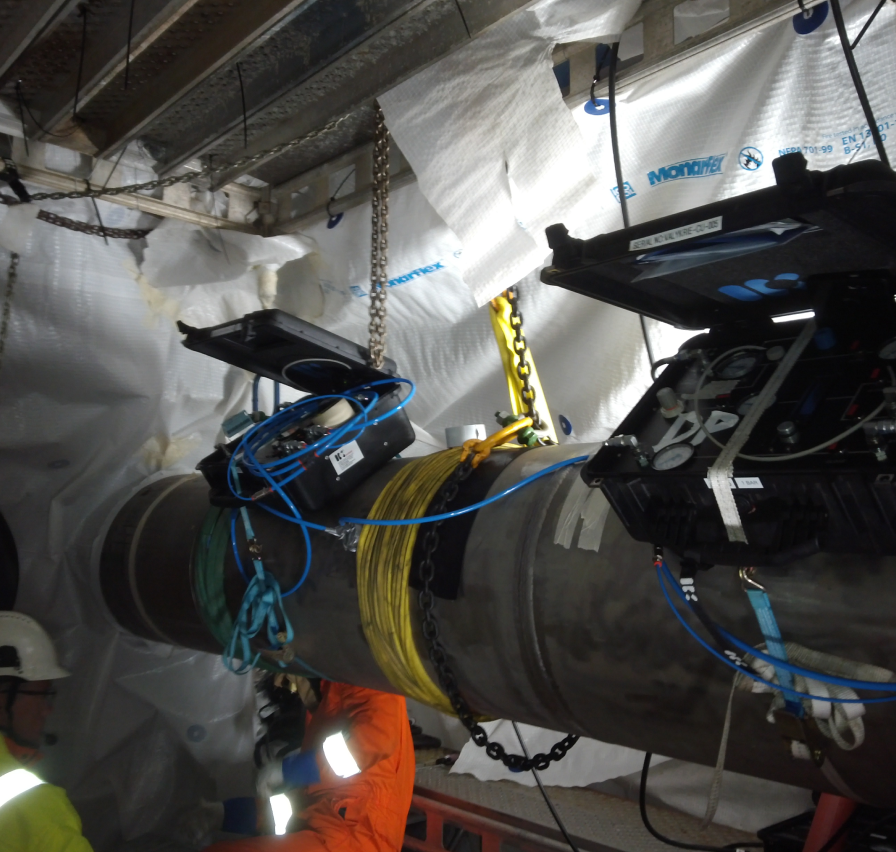
Flushing of the system would require the removal of all subcontractor-installed components and several months of pressure testing and drying of the pipeline system. The availability of fresh water for flushing would also present significant challenges, as would the requirement to clamp down all pipe supports, tighten all bolts, punch off, and accept all systems.
IK TOPSIDE was tasked with finding an alternative technology which would allow for the efficient back-gas purging of over 132 wells/66 tie-ins, thus avoiding significant delays in the commissioning schedule associated with the planned hook-up program.
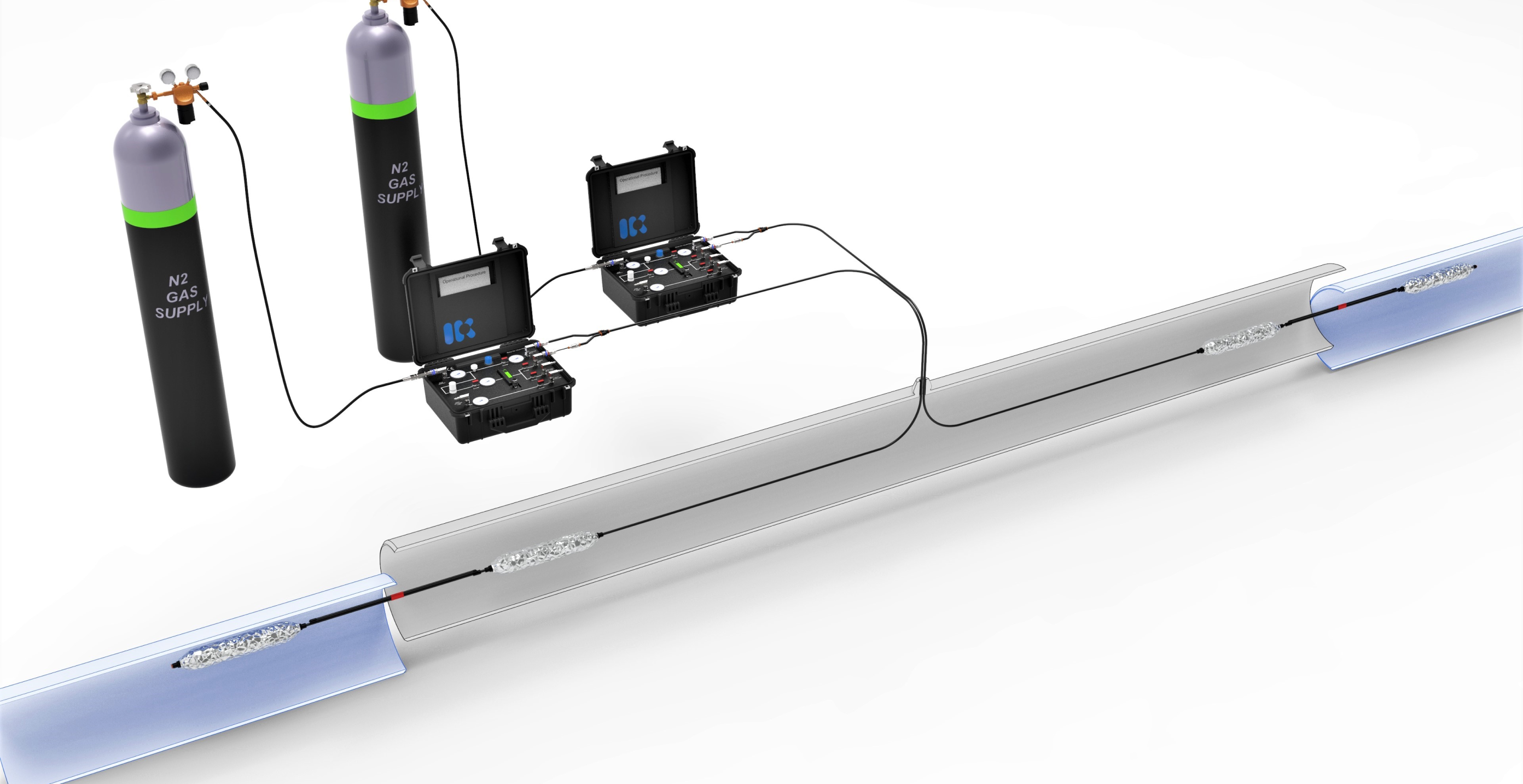
TESTING & PLANNING
Depending upon pipe diameter (anything from 2” – 24”), alternative materials were required for the back-gas system if it was to be successfully removed from a 1” Threadolet in each scenario. Our response was to design three products, allowing a 1” Threadolet to be used, regardless of pipe diameter, thus allowing the client to utilise the accepted engineered piping design.
Each of the three Valkyrie systems utilised a different barrier material, best suited to various pipe dimensions. The foiled film suited to larger pipe sizes was rigorously tested to ensure stability in a more volatile pipeline environment.
A total of eight verification tests were successfully performed using each product in faithfully replicated offshore circumstances, including operation facilities, rigging methods, installation and welding operations, and mock-up repair work during operations.
WHAT WE DID – INNOVATE
Presented with one pipeline scenario, coupling a bridge’s pipelines between two offshore production installations, IK- TOPSIDE responded by developing the Valkyrie System product range, which comprises three back-gas system solutions to service all sizes of pipeline, with the ability to retrieve these via a 1” Threadolet. In just two weeks, we had designed and tested the prototype and were ready to demonstrate it to our client.
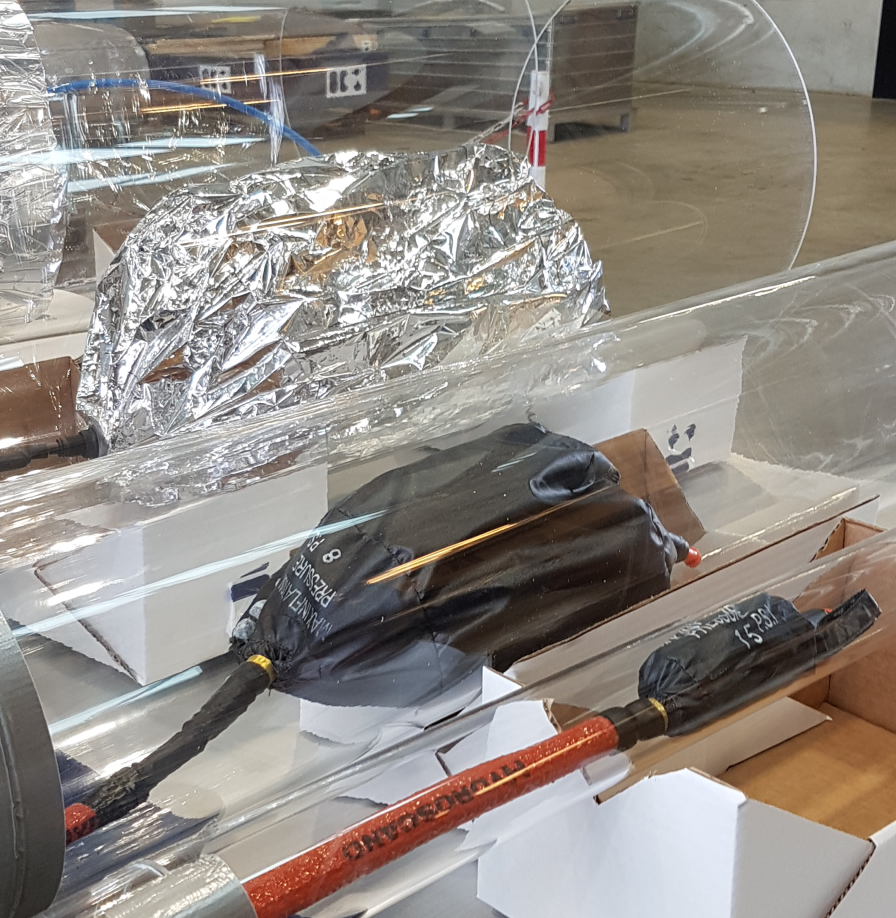
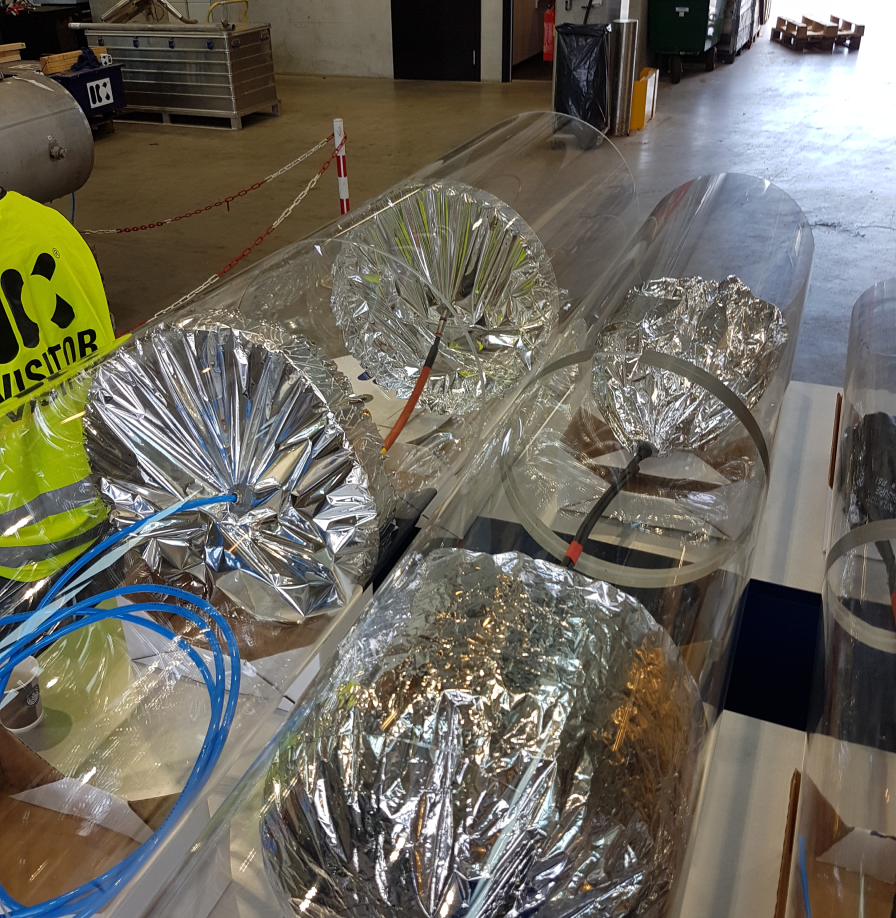
SITE OPERATION
During 2018/2019, IK TOPSIDE deployed the Valkyrie back-gas system on a total of 132 welds, equating to 64 pipe spool tie-ins and connecting the five installations to 4 bridges.
An extremely high-quality weld – well below 100ppm O2 levels – was found to be produced by each Valkyrie system, regardless of pipe size. With operations taking place for 3-4 months every three months during a two-year period, the end client’s commissioning schedule was completed as per initial forecasts.
The Valkyrie Back-Gas Control Unit was utilised throughout, controlling and regulating barrier inflation pressure as well as independent regulation of gas injection. As a “Plug and Play” unit, it enabled efficient installation and operation – critical when considering the volume of welds.
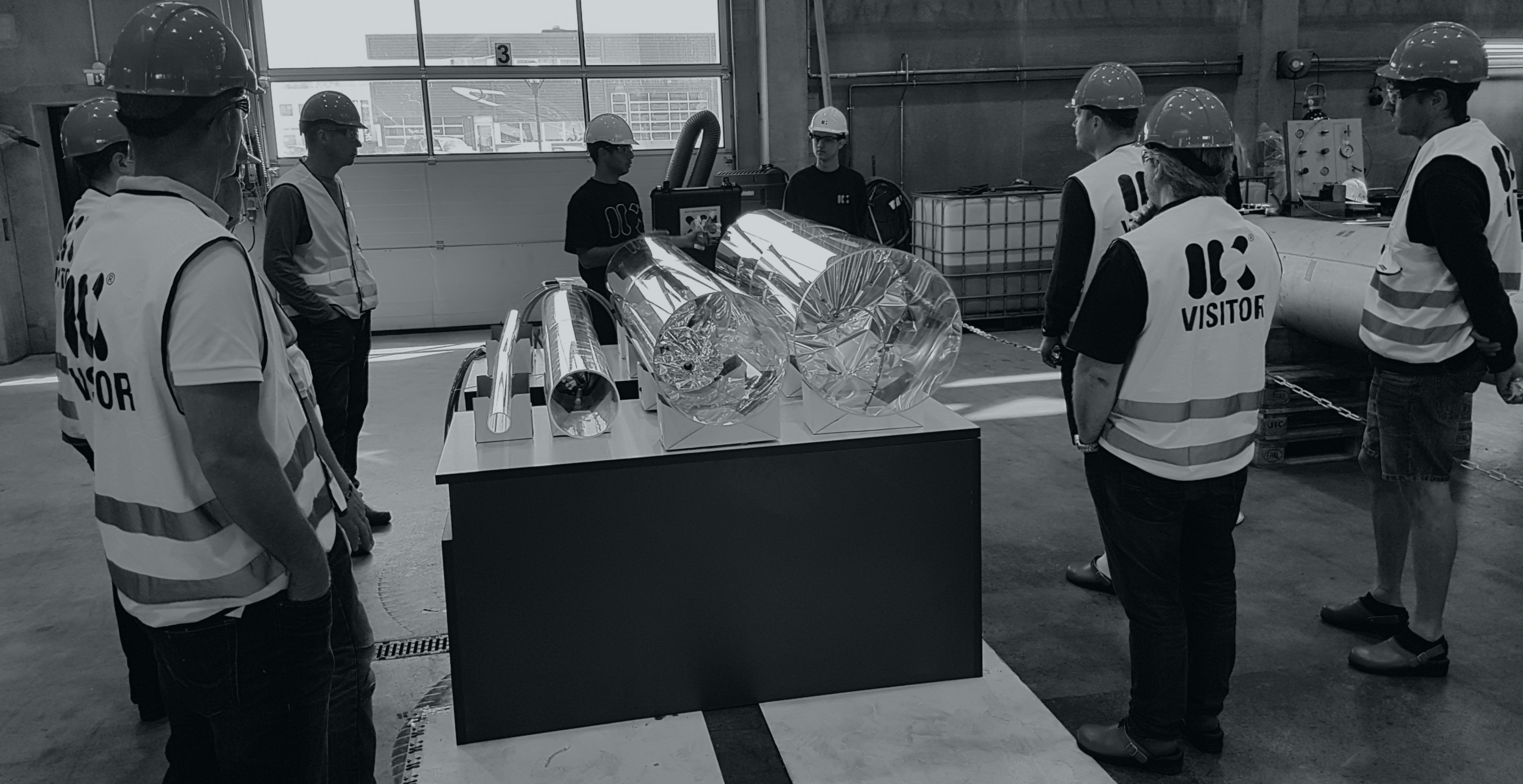